
First we create
THE CAD MODEL
Once we've decided which of the many great engines out there we want to design a keychain for, we need to design a CAD model for later manufacturing. This can take half a day or a whole working day, because we want your key fob to represent your engine as accurately as possible!
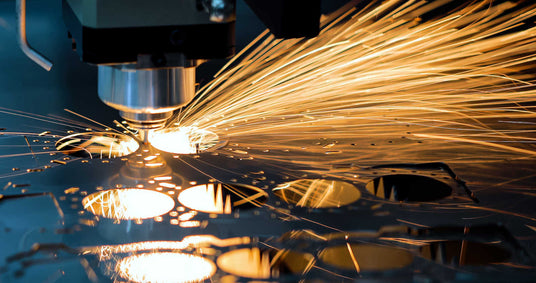
THE
LASER CUTTING
The blanks are the only part of the process that we don't do ourselves (unfortunately the €200,000 for a corresponding machine aren't in our bank account). But this step also happens in Germany. Not cheap, but quality is simply our top priority!
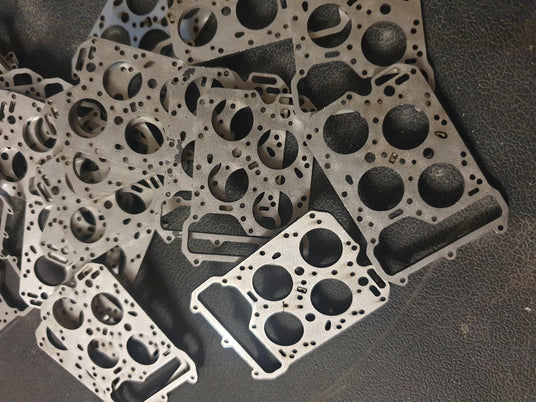
THE
blanks
with whom we then continue to work, still live up to their name... that's why...
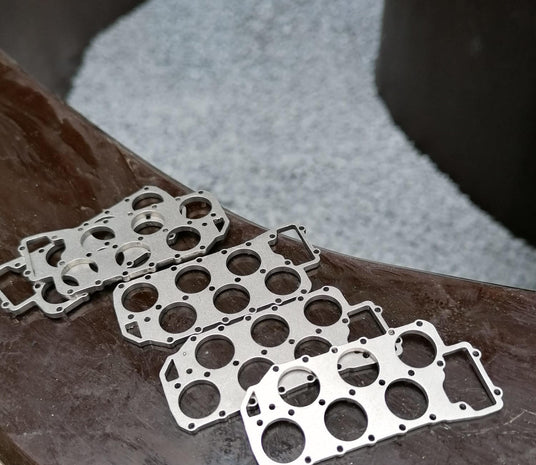
...IN OUR
OWN GRINDING SYSTEM
they get deburred for at least 8 hours (depending on the model), so that in the end they not only look good, but they also feel very high quality when you hold them in your hand later
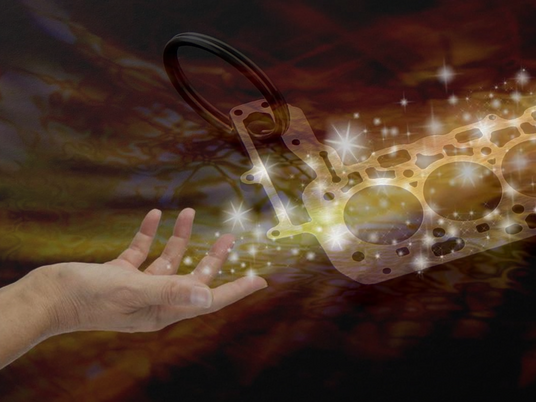
FINALLY
SOME MAGIC!
The penultimate and probably most important step remains our trade secret because it ultimately makes our product incomparable.
Just this much: the production of the brushed surface takes place entirely by hand here with us!
It was a long way until we were able to reproducibly achieve the combination of a beautiful feel with round edges and a brushed surface and it is still a lot of work for each individual pendant, but it is worth it!
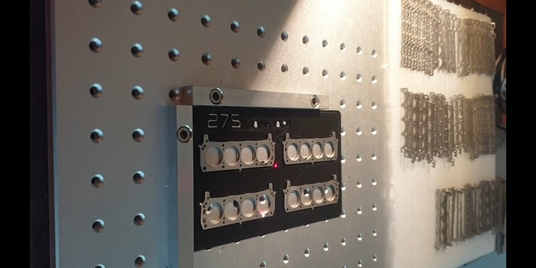
AS
icing on the cake
We provide the head gaskets with our logo using a modern fiber laser and - optionally available for most engines - with an engine-specific engraving.
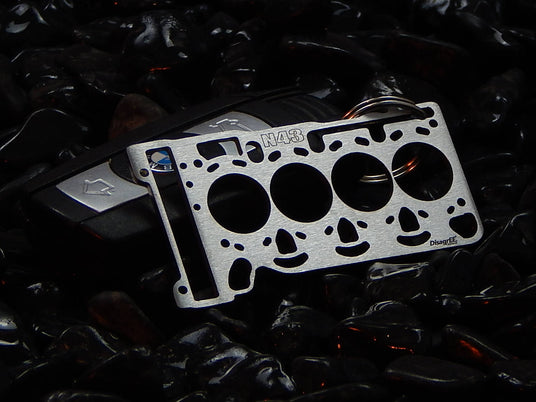
WHAT YOU THEN HOLD
IN YOUR HANDS
is an absolutely unique piece of automotive jewelry made in Germany that suits you and your engine exactly and shows that you love technology and engines and are not satisfied with boring mainstream stuff.